Galling occurs when friction and cohesive attraction occur between two hard, brittle materials. This phenomenon is more prevalent in softer metals like aluminum and stainless steel. These metals have naturally occurring protective oxide films that prevent corrosion and reduce friction when they contact each other. However, these layers are easily rubbed away during the installation of fasteners if excessive pressure and heat is exerted on them. Abrasive wear If hard particles plough a groove into the surface of another material it’s called abrasive wear. This type of wear can occur due to a number of reasons like shear, impact, or friction. This type of wear is common when fastening threaded materials together. Stainless steel is especially prone to galling because it’s relatively soft, which causes more friction between mating surfaces. This then creates a snowball effect, where more friction leads to more deformation, and so on. Other factors that can cause galling include excessive pressure, a lack of proper lubrication, and metal type selection. Some metals, such as aluminum and precipitation hardened stainless steel, are more prone to galling than others. Also, the ductility of the nut or bolt must be taken into account when choosing these components. This can be accomplished by using a shot peened surface on the bolt or by selecting a higher grade of stainless steel for the nut. Heat damage When metals come into contact under high loads, they experience an increased level of friction. This can cause adhesive wear and galling. Galling can also damage threaded fasteners and lead to seizing. This is a serious complication that can lead to expensive repairs and schedule delays. The occurrence of galling is influenced by the surface condition of the contacting materials, their hardness and ductility, lubrication, and temperature. A passive chromium oxide layer and the alloying elements in stainless steels make them more resistant to galling than other metals, but the type of material used in the application is also critical. For example, shot peened stainless-on-stainless steel is more resistant to galling than annealed or strain hardened steels. Moreover, the use of dry film lubricant coatings reduces the likelihood of galling. Also, lowering the wrench speed during installation and removal will reduce the amount of heat generated. This will reduce the chances of galling and prevent it from becoming a problem. Debris buildup As the friction between a bolt and nut gets higher, more debris is introduced to the surfaces that are rubbing together. These particles create even more heat and cause further friction. This snowball effect can eventually cause the materials to weld together, which is known as galling. Galling can happen with all metals, although stainless steel hardware is particularly prone to it. To reduce the chance of galling, lubricate the fasteners during installation. However, it’s important to use a lubricant that is compatible with the fasteners and the environment. For example, food industry applications may require a non-toxic anti-seize solution like molybdenum. In addition to lubrication, slowing down the tightening process can help prevent galling. The friction generated by power tools can heat the fasteners and increase the likelihood of galling. The use of coarse threads or cold rolled surfaces can also lower the risk of galling. Lastly, it is important to inspect the surface of a fastener before using it to ensure it’s free of defects that could contribute to galling. Bonding Unlike other types of wear, galling is a type of adhesion that can cause surface materials to unintentionally adhere to each other. It results in the transfer of material from one surface to another and typically appears as a gouge or score mark that terminates into a mound of metallic residue. A severe form of adhesive wear, galling can be caused by high loads, hard surfaces, and lack of lubrication. Some metals are more susceptible to galling than others, including aluminum and stainless steel. This is because softer materials can generate more heat and a protective oxide layer during friction. The best way to reduce the chance of galling is to choose a harder, more wear-resistant alloy. Additionally, electropolishing your threads can smooth rough surface finishes and reduce the possibility of galling. In addition, reducing the torque speed during installation can reduce the amount of heat generated. This will also allow the heat to dissipate more quickly.what is galling
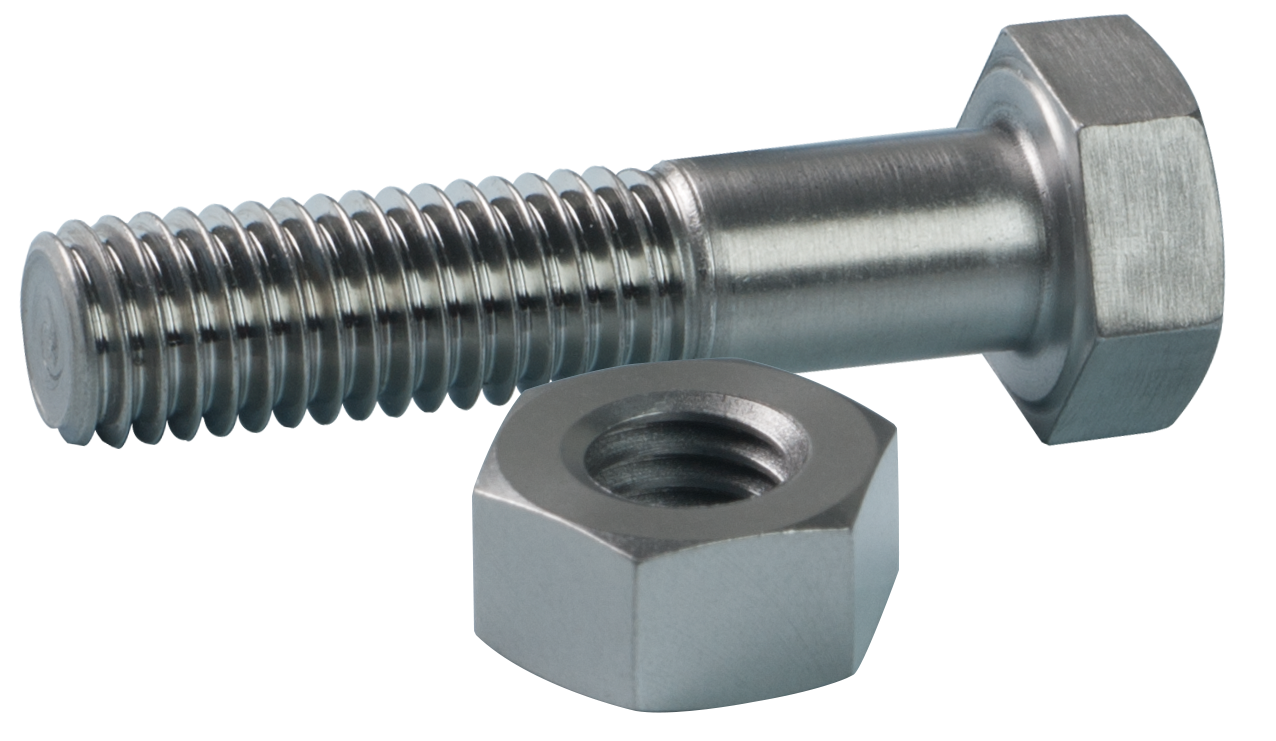